Ingersoll 648 Bypass Is Too Low
-
- Posts: 178
- Joined: Sun Mar 21, 2021 8:03 pm
- Location: Hemlock, MI
- Has thanked: 20 times
- Been thanked: 645 times
Ingersoll 648 Bypass Is Too Low
I have had this Ingy 648 for a couple of years now. For me, there are always known issues.
I already tore into the running engine to get it from running to running right. I missed an issue that I cannot believe I missed. The oil filter gasket that is used to mount the oil filter to the engine will often leak. This is not the rubber seal to the shroud that costs $10ish and has caused probably half of the engine failures for Onan engines that use them. So, this gasket and the mounting bolts are under the front shroud. I will get to that one day, but it sure does urk me that I did not do it. I keep two gaskets in my box because the leak is so common. The first gasket used was cork. They all leak at this point. The newer material gaskets should never leak. But, if you do not do it right...
That was not my point. My 648 is bypassing at 1,500 psi, which means that even using the power steering makes it squeal. The 648 comes with a holding valve. The holding valve makes it impossible to get at the bypass cover nut. I had already dropped the oil when I checked the one-model-only factory filter screen for the loaders before the 4-digits. I found a lot of rubbery material in the filter. I also noticed that the curl function was flopping in one direction. I then looked at the parts diagram and saw that the curl cylinder had a rather large seal that I easily connected to what I had found.
I need to bench-test the bypass with the hydraulic system that is now open for access. Could there be seal debris in there? Or has the bypass setting been wrong all these years? I am betting the setting has been wrong all these years. I left the test gauge on the tractor for almost a year after cleaning out the filter screen. The bypass is exactly at 1,500. It was never lower or higher. But since I am bench-testing it, the jump to removing the bypass stuff is pretty straightforward.
The bench test oil pump procedure is on page 17 of the Case hydraulic test manual. I have the exact grease gun the manual calls for. But I have to go from 1/8" NPT to the JIC 12 (I think: edit it is a JIC 10 as are most of the bigger hose fittings) of the oil input on the control valve with the work ports capped.
It all seems straightforward. Has anyone done this before?
The strange but kind of assuring thing is I had saved a link that showed that you could reach the adjuster screw through a hole in the frame. And this was on a 648. And this other 648 also had exactly 1,500 psi at the bypass. He kind of left it dangling. His 648 was an early version and did not have the holding valve in the way. I have the later version of the 648, and my version has the external holding valve as standard. This other guy was able to access his bypass cover nut with the hydraulic system intact and used the test port gauge to check it as he went a quarter turn at a time. He reached 3/4 of a turn and was close to 2,400 psi. And then, nothing.
I already tore into the running engine to get it from running to running right. I missed an issue that I cannot believe I missed. The oil filter gasket that is used to mount the oil filter to the engine will often leak. This is not the rubber seal to the shroud that costs $10ish and has caused probably half of the engine failures for Onan engines that use them. So, this gasket and the mounting bolts are under the front shroud. I will get to that one day, but it sure does urk me that I did not do it. I keep two gaskets in my box because the leak is so common. The first gasket used was cork. They all leak at this point. The newer material gaskets should never leak. But, if you do not do it right...
That was not my point. My 648 is bypassing at 1,500 psi, which means that even using the power steering makes it squeal. The 648 comes with a holding valve. The holding valve makes it impossible to get at the bypass cover nut. I had already dropped the oil when I checked the one-model-only factory filter screen for the loaders before the 4-digits. I found a lot of rubbery material in the filter. I also noticed that the curl function was flopping in one direction. I then looked at the parts diagram and saw that the curl cylinder had a rather large seal that I easily connected to what I had found.
I need to bench-test the bypass with the hydraulic system that is now open for access. Could there be seal debris in there? Or has the bypass setting been wrong all these years? I am betting the setting has been wrong all these years. I left the test gauge on the tractor for almost a year after cleaning out the filter screen. The bypass is exactly at 1,500. It was never lower or higher. But since I am bench-testing it, the jump to removing the bypass stuff is pretty straightforward.
The bench test oil pump procedure is on page 17 of the Case hydraulic test manual. I have the exact grease gun the manual calls for. But I have to go from 1/8" NPT to the JIC 12 (I think: edit it is a JIC 10 as are most of the bigger hose fittings) of the oil input on the control valve with the work ports capped.
It all seems straightforward. Has anyone done this before?
The strange but kind of assuring thing is I had saved a link that showed that you could reach the adjuster screw through a hole in the frame. And this was on a 648. And this other 648 also had exactly 1,500 psi at the bypass. He kind of left it dangling. His 648 was an early version and did not have the holding valve in the way. I have the later version of the 648, and my version has the external holding valve as standard. This other guy was able to access his bypass cover nut with the hydraulic system intact and used the test port gauge to check it as he went a quarter turn at a time. He reached 3/4 of a turn and was close to 2,400 psi. And then, nothing.
Last edited by ssmewing on Wed Oct 16, 2024 1:31 pm, edited 2 times in total.
-
- Posts: 178
- Joined: Sun Mar 21, 2021 8:03 pm
- Location: Hemlock, MI
- Has thanked: 20 times
- Been thanked: 645 times
Re: Ingersoll 448 Bypass Is Too Low
https://photos.app.goo.gl/FNyBw7hQR5Sit9ZS7

I am trying to post a video. I use Google and Android. So, I am not sure that this will work for you. It worked for me, but I have the program that created it and the file is on my account.
I am trying to post a video. I use Google and Android. So, I am not sure that this will work for you. It worked for me, but I have the program that created it and the file is on my account.
-
Spike188
- Posts: 1196
- Joined: Sat Mar 06, 2021 12:58 pm
- Location: Ayr Ontario
- Has thanked: 7318 times
- Been thanked: 4730 times
Re: Ingersoll 448 Bypass Is Too Low
@ssmewing The video works for me. Thanks for posting. That is another winter project on our 646.
Spike Colt - 9 & 10, Case - 108, 118, 444, 446, 448, 646, 646bh, Ingersoll 4016, 4118AH
-
- Posts: 178
- Joined: Sun Mar 21, 2021 8:03 pm
- Location: Hemlock, MI
- Has thanked: 20 times
- Been thanked: 645 times
Re: Ingersoll 448 Bypass Is Too Low
As you all know, doing one thing leads to another. They should write a song for this.
https://youtu.be/JHYIGy1dyd8?si=1mUwgTAkoaOQUt9n
I hated this period of rock. I was an MTV watcher, though. I just never bought any of this crap for music.
I re-entered the love of rock when the 90s exploded with plenty of talent, and I was once again buying music. So, yay, I am a 62-year-old guy you will hear at the stoplight with Metallica cranked as high as it will go. My current vehicle is the first one I have had that I did not build the sound system in, which actually rattles the rear-view mirror.
I still have not adjusted the bypass setting. How the guy on casecoltingersoll could ever see the bypass screw through the whole in the frame is beyond me. I will be bench-testing the valve.
The 3 point control has detents for float as you all would know. My detent has dirty balls and the force required is too high and that can and does cause issues if ignored. On the bench fixing that is easy.
I also removed all the hoses and saw how bad they were. I realize now that Case or its dealers used pretty cheap hoses. The outer cover is nothing but rubber. There is no outer protection with a woven and reinforced outer cover that is so common now.
The installer of the rear PTO valve must not have realized that the valve did come with 90s for all 4 ports and those 90s are meant to be adjusted for hose installation. I will be replacing the hoses with higher quality but spending way less on hose ends that are very expensive and I will have a better result and less rubbing. I will be ordering all my hoses from one place. Remind me to scan and upload the invoice. If any of you at some point ever need to replace the same hoses then it will save you some time.
Getting that valve out is a test of my strength, that is for sure. That return fitting is a 1 1/4" nut and I had to maneuver myself to where I could get my feet on the inside of the frame rail so I could pull harder on that wrench. All I have left to break loose is the power beyond port. Then hopefully, the two mounting screws are agreeable to coming off.
The other thing that is down there is the banana plate and its components. I have the first edition of an improved plate. The plate is good and will be re-installed. The swivel bushing to the pedal rod is in need of replacement and is still available. I have the parts for the direction control pivot point. My friction disk had gone bad early this spring. I already have that. The plate was very close to completely spot-on and the traveler has been causing very little wear to itself and the plate.
The install kits come with a plain bolt, lock washer, and nut. A tip for you is to use serrated flanged bolts and plain flanged or standard nuts are fine to use. The special bolt head acts like having someone holding the bolt head with a wrench for you when you want to lock it down. Once the nut is finger-tight, any method you use to tighten the nut can be done from inside and under the tractor with ease because the bolt will bite and stay.
I have psoriatic arthritis and other issues. I still have a fair bit of my strength. But it gets more painful to get up and down after a while. I will not enjoy my evening once I sit still in my comfy recliner, which is the good part. The bad part is how bad my hips, knees, and feet will hurt when I get up out of the comfy chair. I guess I should be happy that I can still work on stuff that requires me to get up and down like that. I know others who are only a few years older than me that cannot do that anymore.
This is the chainsaw blender that I had built out of a chainsaw. It was one of those April days that was just gorgeous, and I did not have all these endless projects back then. I have seen the pre-built blenders, but I do not use pre-built ones. That blender has made an awful lot of Margaritas and other drinks for nearly 40 years now. This year was the first year that I had to go back and fix something. The salvage fuel tank I used to keep the fill at the same angle as the blender had failed at the fuel line port. I have only used Amsoil for the fuel mixture, and no matter how many years it sat, it always jumped back to life, and I have never had to go into the carb and clean it. I have a new tank to install, and of course, the Hemlock Case Guy always replaces the old fuel line. My 20-year-old son will have it to entertain him and his friends now. I could not find one of the many videos. I always ran the blender. I got my Ted Nugent on and played the chainsaw like a guitar. At this event, my brother-from-another-mother kept the glasses filled. This event was an endurance fundraiser for Leader Dogs for the Blind. We were in Traverse City. This was back when I could ride 350 miles over three days on Lake Michigan on my PWC and still walk afterward. The US Coast Guard would often honor us with a morning partial run with us. One year, the morning that they spent the night at was a very high wave situation, and they had to stay at the dock. We ride no matter what unless it is lightning. I had a place on Lake Huron and used to ride there, but only when it was a small craft advisory. I am not joking. I was the only boat out there. I had to choose my bearings based on the wind. If my craft lost the engine, the engine was hopped up pretty good and sometimes I would blow it up, I had to point myself in the direction that I would get blown back to Michigan, not Canada. I also was hoping to reach the deeper water for the better waves. I needed at least 40 feet of water, and I was on the edge of Saginaw Bay, which was not very deep. I would run the boat until the fuel light came on and then head back to the dock.

https://youtu.be/JHYIGy1dyd8?si=1mUwgTAkoaOQUt9n
I hated this period of rock. I was an MTV watcher, though. I just never bought any of this crap for music.
I re-entered the love of rock when the 90s exploded with plenty of talent, and I was once again buying music. So, yay, I am a 62-year-old guy you will hear at the stoplight with Metallica cranked as high as it will go. My current vehicle is the first one I have had that I did not build the sound system in, which actually rattles the rear-view mirror.
I still have not adjusted the bypass setting. How the guy on casecoltingersoll could ever see the bypass screw through the whole in the frame is beyond me. I will be bench-testing the valve.
The 3 point control has detents for float as you all would know. My detent has dirty balls and the force required is too high and that can and does cause issues if ignored. On the bench fixing that is easy.
I also removed all the hoses and saw how bad they were. I realize now that Case or its dealers used pretty cheap hoses. The outer cover is nothing but rubber. There is no outer protection with a woven and reinforced outer cover that is so common now.
The installer of the rear PTO valve must not have realized that the valve did come with 90s for all 4 ports and those 90s are meant to be adjusted for hose installation. I will be replacing the hoses with higher quality but spending way less on hose ends that are very expensive and I will have a better result and less rubbing. I will be ordering all my hoses from one place. Remind me to scan and upload the invoice. If any of you at some point ever need to replace the same hoses then it will save you some time.
Getting that valve out is a test of my strength, that is for sure. That return fitting is a 1 1/4" nut and I had to maneuver myself to where I could get my feet on the inside of the frame rail so I could pull harder on that wrench. All I have left to break loose is the power beyond port. Then hopefully, the two mounting screws are agreeable to coming off.
The other thing that is down there is the banana plate and its components. I have the first edition of an improved plate. The plate is good and will be re-installed. The swivel bushing to the pedal rod is in need of replacement and is still available. I have the parts for the direction control pivot point. My friction disk had gone bad early this spring. I already have that. The plate was very close to completely spot-on and the traveler has been causing very little wear to itself and the plate.
The install kits come with a plain bolt, lock washer, and nut. A tip for you is to use serrated flanged bolts and plain flanged or standard nuts are fine to use. The special bolt head acts like having someone holding the bolt head with a wrench for you when you want to lock it down. Once the nut is finger-tight, any method you use to tighten the nut can be done from inside and under the tractor with ease because the bolt will bite and stay.
I have psoriatic arthritis and other issues. I still have a fair bit of my strength. But it gets more painful to get up and down after a while. I will not enjoy my evening once I sit still in my comfy recliner, which is the good part. The bad part is how bad my hips, knees, and feet will hurt when I get up out of the comfy chair. I guess I should be happy that I can still work on stuff that requires me to get up and down like that. I know others who are only a few years older than me that cannot do that anymore.
This is the chainsaw blender that I had built out of a chainsaw. It was one of those April days that was just gorgeous, and I did not have all these endless projects back then. I have seen the pre-built blenders, but I do not use pre-built ones. That blender has made an awful lot of Margaritas and other drinks for nearly 40 years now. This year was the first year that I had to go back and fix something. The salvage fuel tank I used to keep the fill at the same angle as the blender had failed at the fuel line port. I have only used Amsoil for the fuel mixture, and no matter how many years it sat, it always jumped back to life, and I have never had to go into the carb and clean it. I have a new tank to install, and of course, the Hemlock Case Guy always replaces the old fuel line. My 20-year-old son will have it to entertain him and his friends now. I could not find one of the many videos. I always ran the blender. I got my Ted Nugent on and played the chainsaw like a guitar. At this event, my brother-from-another-mother kept the glasses filled. This event was an endurance fundraiser for Leader Dogs for the Blind. We were in Traverse City. This was back when I could ride 350 miles over three days on Lake Michigan on my PWC and still walk afterward. The US Coast Guard would often honor us with a morning partial run with us. One year, the morning that they spent the night at was a very high wave situation, and they had to stay at the dock. We ride no matter what unless it is lightning. I had a place on Lake Huron and used to ride there, but only when it was a small craft advisory. I am not joking. I was the only boat out there. I had to choose my bearings based on the wind. If my craft lost the engine, the engine was hopped up pretty good and sometimes I would blow it up, I had to point myself in the direction that I would get blown back to Michigan, not Canada. I also was hoping to reach the deeper water for the better waves. I needed at least 40 feet of water, and I was on the edge of Saginaw Bay, which was not very deep. I would run the boat until the fuel light came on and then head back to the dock.

-
- Posts: 178
- Joined: Sun Mar 21, 2021 8:03 pm
- Location: Hemlock, MI
- Has thanked: 20 times
- Been thanked: 645 times
Re: Ingersoll 448 Bypass Is Too Low
I just noticed I titled this post wrong. 648 not 448.
So, I bought the adaptors and a check valve to bench-test the bypass. I would have never thought that you could fill a grease gun with oil and pump that out. Now I know.
I struggled to get a reading. I could pump it up, but it did not ever come close to holding at the high pressures. I think I may have needed a higher-pressure check valve. What I ended up doing was, as I kept pumping, I looked for what I was getting as a peak pressure. When I got it to where it would not read higher than 2,400, briefly, it was my issue. That was where I felt I should be. My concern is that when I checked how many turns out that was, it was only about 3/4s of a turn from all the way in. And, I forgot to check how many turns I was at when I started. That was a big mistake as I had a known, and I did not record that known. So, I was at 1,500 psi, but I do not know how many turns that was on the adjuster. I do this when I work on carbs before I take them apart. So, I was pretty perturbed by my mistake.
What a mess that was. The work ports are capped, and then you clamp the spool to simulate a stalled work position. You pump into the input and leave the output open. Everytime I went past the bypass it would let oil out. I think I have it too high now. If it had the right check valve I think it would have been easy. The grease gun model that the manual called for has a check valve. That model ran about $150. When I was ordering my adapters I ordered a check valve. But, the check valve may not have been for the higher psi I was looking at. Hand-pumping it, I could go past the 3,000 on my test gauge, which is another thing that I would not have thought a grease gun could do. Maybe it was because they were American-made.
If I put it back to its running condition that puts the holding valve back and there is no way I can get the cover nut off or on with that holding valve in the way.
So, I bought the adaptors and a check valve to bench-test the bypass. I would have never thought that you could fill a grease gun with oil and pump that out. Now I know.
I struggled to get a reading. I could pump it up, but it did not ever come close to holding at the high pressures. I think I may have needed a higher-pressure check valve. What I ended up doing was, as I kept pumping, I looked for what I was getting as a peak pressure. When I got it to where it would not read higher than 2,400, briefly, it was my issue. That was where I felt I should be. My concern is that when I checked how many turns out that was, it was only about 3/4s of a turn from all the way in. And, I forgot to check how many turns I was at when I started. That was a big mistake as I had a known, and I did not record that known. So, I was at 1,500 psi, but I do not know how many turns that was on the adjuster. I do this when I work on carbs before I take them apart. So, I was pretty perturbed by my mistake.
What a mess that was. The work ports are capped, and then you clamp the spool to simulate a stalled work position. You pump into the input and leave the output open. Everytime I went past the bypass it would let oil out. I think I have it too high now. If it had the right check valve I think it would have been easy. The grease gun model that the manual called for has a check valve. That model ran about $150. When I was ordering my adapters I ordered a check valve. But, the check valve may not have been for the higher psi I was looking at. Hand-pumping it, I could go past the 3,000 on my test gauge, which is another thing that I would not have thought a grease gun could do. Maybe it was because they were American-made.
If I put it back to its running condition that puts the holding valve back and there is no way I can get the cover nut off or on with that holding valve in the way.
-
- Posts: 178
- Joined: Sun Mar 21, 2021 8:03 pm
- Location: Hemlock, MI
- Has thanked: 20 times
- Been thanked: 645 times
Re: Ingersoll 648 Bypass Is Too Low
I am pretty certain I am going to have to adjust the bypass after I have this thing put back together. I think that while I am able to get to the installed in the tractor valve but without the holding valve in the way, I am going to figure out how to remove a 3/4" cover nut, then a deep socket needed for the adjuster screw set nut, and lastly the adjuster is an extra large flat blade. The flat blade can be another socket.
Today, I will check to see if a 1/4" socket extension will fit through the hole in the rear of the frame that is lined up with the bypass nut. Then does a 1/4" drive socket in 3/4" exist in a deep socket?
Today, I will check to see if a 1/4" socket extension will fit through the hole in the rear of the frame that is lined up with the bypass nut. Then does a 1/4" drive socket in 3/4" exist in a deep socket?
-
Spike188
- Posts: 1196
- Joined: Sat Mar 06, 2021 12:58 pm
- Location: Ayr Ontario
- Has thanked: 7318 times
- Been thanked: 4730 times
Re: Ingersoll 648 Bypass Is Too Low
Steve, thank you for walking us through the adjustment. I will follow your lead when time is available to set the pressure on a 646L and 646BJH. It looks like this is more than a 30 minute job. 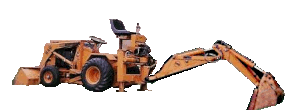
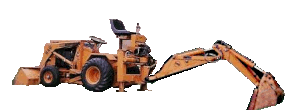
Spike Colt - 9 & 10, Case - 108, 118, 444, 446, 448, 646, 646bh, Ingersoll 4016, 4118AH
-
- Posts: 178
- Joined: Sun Mar 21, 2021 8:03 pm
- Location: Hemlock, MI
- Has thanked: 20 times
- Been thanked: 645 times
Re: Ingersoll 648 Bypass Is Too Low
Well, the 1/4" extensions do not fit through the hole. I already knew this due to reading so much and then saving past posts from casecoltingersoll. I had bought a very long flat screwdriver that does fit after I grinded the flares off that are wider than the business end. I will be able to turn the adjustment screw.ssmewing wrote: ↑Wed Oct 16, 2024 1:41 pm I am pretty certain I am going to have to adjust the bypass after I have this thing put back together. I think that while I am able to get to the installed in the tractor valve but without the holding valve in the way, I am going to figure out how to remove a 3/4" cover nut, then a deep socket needed for the adjuster screw set nut, and lastly the adjuster is an extra large flat blade. The flat blade can be another socket.
Today, I will check to see if a 1/4" socket extension will fit through the hole in the rear of the frame that is lined up with the bypass nut. Then does a 1/4" drive socket in 3/4" exist in a deep socket?
The cap is right at the back edge of the center floorboard. I may have to buy some hoses for the drive motor so I can delete the holding valve. I will put it all back together with the holding valve. It is not hard to remove. The mess is worse than anything. During my bench testing, I did find that the adjuster screw leaks a lot of oil. The small nut to lock up the screw has a metal seal, and the cap nut has the same. It does leak if the cap nut is not installed.
I may look at making a slot in the end of the cap nut. It will not work to break it loose or tighten it down, but there is a lot of threading to unscrew it, and the slot would make one part of it easier.
-
Harry
- Posts: 1780
- Joined: Sun Mar 07, 2021 8:33 am
- Location: Lockport,NY
- Has thanked: 10860 times
- Been thanked: 7649 times
Re: Ingersoll 648 Bypass Is Too Low
Thanks for the update Steve. This is something I need to look at on the 646. This winter it will be in the shop for a cab installation project.
Harry

1973 444, 1974 644, 1976 446, 1977 646, 1986 226
-
- Posts: 178
- Joined: Sun Mar 21, 2021 8:03 pm
- Location: Hemlock, MI
- Has thanked: 20 times
- Been thanked: 645 times
Re: Ingersoll 648 Bypass Is Too Low
https://photos.app.goo.gl/7umkNx8q2G1bUQLH6
I'm sorry the video was so shaky. I had to use Zoom because I did not have the distance to take a steady shot.
https://photos.app.goo.gl/2c8vLnb4gRVPAixM9
To the best of my knowledge, the banana plate in this video is installed about as well as it can be.
I mentioned a tab that I spread from the area of the follower while it is in the reverse position. Someone in this group complained that it was hard getting it out of reverse when they shifted into reverse. What I found earlier and fixed was the follower was coming out of the groove when it was shifted into reverse and then was getting pinched between the tab on the banana plate mount and the groove. The fix was bending the mounting plate and getting it perfectly square. It was not perfectly square when I checked it.
Then, when I re-mounted the holder, I adjusted the banana plate holder to stay perfectly in the groove, solving the jamming in reverse. I also figured out how to get out of the jammed reverse position. Pressing the foot pedal a little changes the geometry just enough to free it from reverse.
I'm sorry the video was so shaky. I had to use Zoom because I did not have the distance to take a steady shot.
https://photos.app.goo.gl/2c8vLnb4gRVPAixM9
To the best of my knowledge, the banana plate in this video is installed about as well as it can be.
I mentioned a tab that I spread from the area of the follower while it is in the reverse position. Someone in this group complained that it was hard getting it out of reverse when they shifted into reverse. What I found earlier and fixed was the follower was coming out of the groove when it was shifted into reverse and then was getting pinched between the tab on the banana plate mount and the groove. The fix was bending the mounting plate and getting it perfectly square. It was not perfectly square when I checked it.
Then, when I re-mounted the holder, I adjusted the banana plate holder to stay perfectly in the groove, solving the jamming in reverse. I also figured out how to get out of the jammed reverse position. Pressing the foot pedal a little changes the geometry just enough to free it from reverse.