Linde 225 MIG welder in bad shape
-
MattA
- Posts: 1026
- Joined: Sun Mar 07, 2021 1:57 pm
- Location: Swansea MA
- Has thanked: 3 times
- Been thanked: 4496 times
-
- Posts: 5280
- Joined: Wed Mar 03, 2021 2:52 pm
- Location: Port Mcnicoll, Ontario
- Has thanked: 12888 times
- Been thanked: 16930 times
- Contact:
Re: Linde 225 MIG welder in bad shape
Had a minor success yesterday with this welder but didn't get a chance to take pictures, I only have the story to tell.
When plugged in there were two obvious problems: the big fan at the rear of the unit did not turn, and the wire feed did not work when the button on the gun was depressed.
The fan is working on 230V AC, and is pretty big, won't be so easy to find a replacement. But more concerning was the wire feed not working. It has a geared, pretty beefy motor, about 4" diameter and 7" tall. On to some troubleshooting. The wire speed is adjusted from a potentiometer on a circuit board with some solid state components: three transistors, some resistors, diodes, and a capacitor. This is hooked via 8 wires to various parts of the machine, through a multi-wire connector. After some goggling the various connections it seemed to me that 24V from a transformer feeds the whole wire speed control mechanism. What I found strange was a component I haven't seen before, a rectifier bridge with 6 pins. The regular four pins, two for AC input ~ ~, - + as negative and positive output, and two pins marked G1 and G2. After some searches it turns out that this is a half-controlled rectifier. A regular rectifier bridge has four diodes, whereas this device has two diodes and two thyristors. A thyristor is like a diode, allowing current to flow only in one direction, but it will only do so when its gate is triggered, and therefore you can turn it on and off. This controlled bridge rectifier is the main power component for controlling the speed of the motor that turns the wire spool when you press on the MIG gun button. My fear that the motor is fried was easily put at rest, when I applied 12V from a battery charger to the motor and it turned. The controlled rectifier bridge was not so easy to troubleshoot. The voltmeter didn't help, so I pulled out the oscilloscope. Hooked up a 24V transformer that I had around, and powered that part of the circuit. I really didn't want to work on this plugged into 240V if at all possible. After some intense and long staring, pondering, and poking of various things, I noticed that the waves on the oscilloscope would change when the multi-wire connector on the circuit board was wiggled. Looking at it more carefully showed multiple pins no longer soldered to the board, cold connection. Re-soldered properly all pins, and the wire speed mechanism works fine. Easy fix, not so easy to find the problem. It was an enjoyable mystery to solve.
Maybe some of you may be wondering about various aspects about this forum. I am as convinced as I was the day it was created, to keep on going with it. Besides offering a (second) home to the Case garden tractor enthusiasts, for me it is also useful to record somewhere the process of fixing my tractors, and all that comes with it. For instance this MIG welder will be used to fix or build something for the tractors. We live in the age of finding a lot of information on the internet, and over the years it has helped me tremendously to find how someone dealt with an issue I was facing. Sometimes you cannot find any info, as is the case with this MIG welder. Maybe my journal of fixing it will help someone else one day. It also helps me remember in a couple of years what I did. And this concludes my ramble
When plugged in there were two obvious problems: the big fan at the rear of the unit did not turn, and the wire feed did not work when the button on the gun was depressed.
The fan is working on 230V AC, and is pretty big, won't be so easy to find a replacement. But more concerning was the wire feed not working. It has a geared, pretty beefy motor, about 4" diameter and 7" tall. On to some troubleshooting. The wire speed is adjusted from a potentiometer on a circuit board with some solid state components: three transistors, some resistors, diodes, and a capacitor. This is hooked via 8 wires to various parts of the machine, through a multi-wire connector. After some goggling the various connections it seemed to me that 24V from a transformer feeds the whole wire speed control mechanism. What I found strange was a component I haven't seen before, a rectifier bridge with 6 pins. The regular four pins, two for AC input ~ ~, - + as negative and positive output, and two pins marked G1 and G2. After some searches it turns out that this is a half-controlled rectifier. A regular rectifier bridge has four diodes, whereas this device has two diodes and two thyristors. A thyristor is like a diode, allowing current to flow only in one direction, but it will only do so when its gate is triggered, and therefore you can turn it on and off. This controlled bridge rectifier is the main power component for controlling the speed of the motor that turns the wire spool when you press on the MIG gun button. My fear that the motor is fried was easily put at rest, when I applied 12V from a battery charger to the motor and it turned. The controlled rectifier bridge was not so easy to troubleshoot. The voltmeter didn't help, so I pulled out the oscilloscope. Hooked up a 24V transformer that I had around, and powered that part of the circuit. I really didn't want to work on this plugged into 240V if at all possible. After some intense and long staring, pondering, and poking of various things, I noticed that the waves on the oscilloscope would change when the multi-wire connector on the circuit board was wiggled. Looking at it more carefully showed multiple pins no longer soldered to the board, cold connection. Re-soldered properly all pins, and the wire speed mechanism works fine. Easy fix, not so easy to find the problem. It was an enjoyable mystery to solve.
Maybe some of you may be wondering about various aspects about this forum. I am as convinced as I was the day it was created, to keep on going with it. Besides offering a (second) home to the Case garden tractor enthusiasts, for me it is also useful to record somewhere the process of fixing my tractors, and all that comes with it. For instance this MIG welder will be used to fix or build something for the tractors. We live in the age of finding a lot of information on the internet, and over the years it has helped me tremendously to find how someone dealt with an issue I was facing. Sometimes you cannot find any info, as is the case with this MIG welder. Maybe my journal of fixing it will help someone else one day. It also helps me remember in a couple of years what I did. And this concludes my ramble

-
thebuildist
- Posts: 853
- Joined: Mon Jul 26, 2021 5:09 pm
- Location: Atlanta, ga
- Has thanked: 869 times
- Been thanked: 3467 times
Re: Linde 225 MIG welder in bad shape
Eugen, I couldn't agree more. That's precisely what's so awesome about this particular forum.
Bob
Bob
"Never be afraid to try something new. How hard can it be?"
-
- Posts: 5280
- Joined: Wed Mar 03, 2021 2:52 pm
- Location: Port Mcnicoll, Ontario
- Has thanked: 12888 times
- Been thanked: 16930 times
- Contact:
Re: Linde 225 MIG welder in bad shape
Thank you for the kind words Bob.thebuildist wrote: ↑Sun Oct 16, 2022 1:37 pm Eugen, I couldn't agree more. That's precisely what's so awesome about this particular forum.
Bob
-
Timj
- Posts: 1449
- Joined: Thu Mar 04, 2021 9:57 pm
- Location: Central WI
- Has thanked: 5280 times
- Been thanked: 5063 times
Re: Linde 225 MIG welder in bad shape
Ya, we are all multitaskers, we don't just work/play with our tractors.
Besides if you don't like something or it's not of interest to you, don't read it.
It's all good
Tim

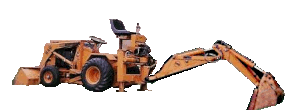
Besides if you don't like something or it's not of interest to you, don't read it.

It's all good





-
- Posts: 1793
- Joined: Sat Apr 23, 2022 8:16 pm
- Location: Missouri
- Has thanked: 13562 times
- Been thanked: 7923 times
Re: Linde 225 MIG welder in bad shape
I agree completely with you guys. I really appreciate being able to come here and not only learn or share things about Case tractors, but many other things that I have found quite interesting, useful, and sometimes downright entertaining!
-
- Posts: 5280
- Joined: Wed Mar 03, 2021 2:52 pm
- Location: Port Mcnicoll, Ontario
- Has thanked: 12888 times
- Been thanked: 16930 times
- Contact:
Re: Linde 225 MIG welder in bad shape
Thanks for being so understanding guys!
soooooo... there IS an update. We were gone all day yesterday, visited my sister, and arrived late. After the kids went to bed, I needed a little time to unwind, and headed to the shed to have a look at that busted fan. A 10 inch diameter, Caravel Rotron fan, made in USA. It made me sad to see this thrown in the garbage.
The motor was not seized, the propeller was turning, but not smoothly. Measured the winding with the ohmmeter, about 90 ohms. This is a reasonable value, not shorted, and not open circuit either. The fan did not turn when hooked on 120V, or 240V. It's a 220V AC fan, but it should turn, just slower, on 120V AC.
At this point I had no expectations of fixing it, but it's fun doing a post mortem too. On to taking it apart, but I was stumped as to how to disassemble it. After many minutes I realized there were two screws/nuts under the label on the back.
Once those nuts were undone the propeller and motor assembly came out of the outer case. But here I got stuck even more. Could find no way of taking the propeller off the shaft.
You know how you don't want to force something and break it, only to find later there was a neat way of disassembly. After enough time staring at it I decided to force the propeller off the shaft. With older equipment I always expect that it's maintainable, and therefore there must be a way to disassemble it neatly. I was surprised to see that the plastic propeller was molded onto the shaft. You will see here on the top of the shaft, that mushroom shape. The propeller has a skirt that goes all around the motor assembly, so it must be taken off to get to the motor. The middle interior of the propeller skirt seems to have been molded around that mushroom, making it impossible to take it off without breaking the plastic, which I did. More on this later.
Once the propeller was taken off, I could take apart the motor, which had four clips holding the top plate. I found two wheel bearings, one the top, and one at the bottom. They were not seized, but turned hard and rough. Some WD40 got them to rotate easily and I got the idea of putting the motor back together just tentatively, and see if it now works on 120V. To my surprise it worked. Amazing, the "thermal protection" that this motor has (inside the winding) seems to work by not allowing the winding to fry if the motor is mechanically seized. Great design! OK, now I realized that the the "heart" of the motor is fine, and all I need is to replace the bearings and fix the propeller somehow.
But it seems the rotor assembly is pressed together, so the bottom wheel bearing would be easy to pull off the shaft, but for the top one to come off I would have to pull the rotor off the shaft, which I am reluctant to do. The bearing at the top can't simply come up the shaft, because of that mushroom shape on the shaft, which seems to be part of the shaft, and not pressed on to it. Being already quite late, but still not ready to stop fooling around, I took the seal off the bearings, washed them well with brake cleaner, blowed them dry, and packed them with some good quality grease.
Standard 608 bearing.
Bearings cleaned.
Repacked.
If the bearings give up on me later, I may as well take the risk and pull them off and replace them, as they are standard 608 wheel bearings.
Here's a short test of the motor on 120V, with the bearings re-packed. At first they wouldn't turn, probably until the grease got spread around. Maybe it's my imagination, but they don't sound smooth like new bearings.
And now, how to fix the plastic propeller. To be continued...
soooooo... there IS an update. We were gone all day yesterday, visited my sister, and arrived late. After the kids went to bed, I needed a little time to unwind, and headed to the shed to have a look at that busted fan. A 10 inch diameter, Caravel Rotron fan, made in USA. It made me sad to see this thrown in the garbage.
The motor was not seized, the propeller was turning, but not smoothly. Measured the winding with the ohmmeter, about 90 ohms. This is a reasonable value, not shorted, and not open circuit either. The fan did not turn when hooked on 120V, or 240V. It's a 220V AC fan, but it should turn, just slower, on 120V AC.
At this point I had no expectations of fixing it, but it's fun doing a post mortem too. On to taking it apart, but I was stumped as to how to disassemble it. After many minutes I realized there were two screws/nuts under the label on the back.
Once those nuts were undone the propeller and motor assembly came out of the outer case. But here I got stuck even more. Could find no way of taking the propeller off the shaft.

Once the propeller was taken off, I could take apart the motor, which had four clips holding the top plate. I found two wheel bearings, one the top, and one at the bottom. They were not seized, but turned hard and rough. Some WD40 got them to rotate easily and I got the idea of putting the motor back together just tentatively, and see if it now works on 120V. To my surprise it worked. Amazing, the "thermal protection" that this motor has (inside the winding) seems to work by not allowing the winding to fry if the motor is mechanically seized. Great design! OK, now I realized that the the "heart" of the motor is fine, and all I need is to replace the bearings and fix the propeller somehow.
But it seems the rotor assembly is pressed together, so the bottom wheel bearing would be easy to pull off the shaft, but for the top one to come off I would have to pull the rotor off the shaft, which I am reluctant to do. The bearing at the top can't simply come up the shaft, because of that mushroom shape on the shaft, which seems to be part of the shaft, and not pressed on to it. Being already quite late, but still not ready to stop fooling around, I took the seal off the bearings, washed them well with brake cleaner, blowed them dry, and packed them with some good quality grease.
Standard 608 bearing.
Bearings cleaned.
Repacked.
If the bearings give up on me later, I may as well take the risk and pull them off and replace them, as they are standard 608 wheel bearings.
Here's a short test of the motor on 120V, with the bearings re-packed. At first they wouldn't turn, probably until the grease got spread around. Maybe it's my imagination, but they don't sound smooth like new bearings.
And now, how to fix the plastic propeller. To be continued...
-
- Posts: 5280
- Joined: Wed Mar 03, 2021 2:52 pm
- Location: Port Mcnicoll, Ontario
- Has thanked: 12888 times
- Been thanked: 16930 times
- Contact:
Re: Linde 225 MIG welder in bad shape
Here's the back of the propeller cleaned up a bit so the steel shaft mushroom fits in.
Drilled the steel shaft with 9/16
Tapped it with an 8-32 and now the propeller is secured to the shaft with a bolt.
Not perfect but better than seeing it thrown in the dump.
-
Spike188
- Posts: 1195
- Joined: Sat Mar 06, 2021 12:58 pm
- Location: Ayr Ontario
- Has thanked: 7259 times
- Been thanked: 4721 times
Re: Linde 225 MIG welder in bad shape
Those bearings pull off with very little effort. I did one recently where the bearing got tight then spun one the shaft. Packed the shaft with jb weld then turned it down. It beat waiting for a repair shop rebuild it.
Spike Colt - 9 & 10, Case - 108, 118, 444, 446, 448, 646, 646bh, Ingersoll 4016, 4118AH
-
- Posts: 5280
- Joined: Wed Mar 03, 2021 2:52 pm
- Location: Port Mcnicoll, Ontario
- Has thanked: 12888 times
- Been thanked: 16930 times
- Contact:
Re: Linde 225 MIG welder in bad shape
After being plugged in for a couple of minutes the fourth capacitor started to spit. 
There goes $12

There goes $12
