Page 1 of 1
loader build resumes!
Posted: Thu Jun 23, 2022 6:18 pm
by thebuildist
Well I have crossed a milestone. After 8 or 9 months and something like 14 long pages, I realized today that the "adding a spool valve" thread can finally be closed.
Yesterday I went ahead and bolted the loader cross member and vertical receivers back onto the tractor. Early this morning I bolted on the transaxle reinforcements and buttoned up the various covers and sheet metal that I had removed in order to get access to the TCV.
So now the tractor is substantially reassembled and I'm ready to continue/finish up the loader build process.
This afternoon I drove out and remounted the loader onto the tractor. That's a bit of a first, because I fabricated the cross member and bolted it on then fabricated the tower receivers and bolted them on then built the loader assembly to match those tower receivers.
But this is the first time that I've completely disassembled everything and then reassembled it and confirmed that the detachable loader can still successfully attach and detach without moving heaven and earth. And it worked fine. There's a bit of grunting and wiggling and pounding with a rawhide faced mallet. But nothing extraordinary or out of order.
So early tomorrow morning I weld up a mounting plate to hold the new spool valve. And as soon as the new valve is bolted in its final position, I have merely to run the various hoses and 3/8 inch hard lines to the four cylinders before, for the first time, the boom and bucket controls will actually work when I pull the levers. It's been such a long road to get to this point it seems impossible. But I'm right on the precipice.
As soon as I can operate the boom and bucket by hydraulics, the final two steps are:
1: Attach the quick attach mounting plates. One to a set of forks, the other to a bucket. I'll have to do some minor fabrication and adjustment to get the quick attach plates on there in the proper orientation. I have yet to work out the full details of the sliding pin that will engage to lock the quick detach implement onto the tractor.
2: The final step will be to work out the balance of how much counterweight I need. And then create the counterweight.
I intend to buy ten 80 lb bags of concrete. I'll load them in the bucket and find the tipping point of how much weight in the bucket causes the back wheels to lift off the ground. From there I'll measure the fulcrum leverage from the center line of the front wheels to where the counterweight will be picked up by the 3-point hitch. And that will tell me how much weight I need slung from the 3-point to keep the back wheels on the ground plus about 500 lb for traction. Whatever weight that is, I'll make a concrete cube with steel shaft ears sticking out the side that I can just slide the rings of the three-point arms right over and lift it up. It seems foolproof to me...
Bob
Re: loader build resumes!
Posted: Thu Jun 23, 2022 8:55 pm
by DavidBarkey
Remember Bob @thebuildist the farther you place the counter weight behind , the less weight you need to use which reduces the over all weight of the tractor and the load on the rear axle . I perfer to split the weight between static and dynamic. Some on / in the wheels and some out back . this reduces stress on the axle in both downward and upward motion of the frame .
BTW Bob , enjoyed reading of your adventures in the build . Job well done .
Re: loader build resumes!
Posted: Fri Jun 24, 2022 10:35 am
by Eugen
Glad you're back tot he loader build. I'm curious what you'll make the hard lines from and how?
Re: loader build resumes!
Posted: Fri Jun 24, 2022 8:21 pm
by thebuildist
I'll make them out of standard 3/8" hydraulic tubing, which I bought at a local hydraulics shop. I picked up some#6 JIC nuts and sleeves on eBay a while back. So all I have to do is bend them and flare them.
For bending 3/8, a little tubing bender works like a charm.
https://m.media-amazon.com/images/I/61j ... _QL65_.jpg
For anything larger I use one of these:
http://www.universaltrading.lk/wp-conte ... bender.jpg
For flaring I've learned as I go. I started by modifying one of these, turning the bevel on its plunger from 45 degrees to 37.
https://content.speedwaymotors.com/Prod ... 69f192.jpg
That was ok for small stuff, but it bent trying to flare 5/8 tubing.
So I bought an eccentric ratcheting flare tool, and modified its plunger.
https://images.cecompass.com/productima ... 808A_A.jpg
That tool is amazing. Instead of ramming the plunger straight in, it rotates the plunger around the inner rim of the tube, like the motion when you rub your finger around a crystal glass to make it ring. So it's only bending a little bit of metal at a time, and progresses around and around, slowly inward until it's all done. Really a pleasure to use, though I did make a twister handle to mount in my drill, so that the drill can do the work of turning the handle the... 50? 75? rotations necessary to finish a 5/8 flare.
Anyway, long ramble to a short question.
If anyone wants to try it themselves, a little advice:. Play a record on repeat while you're working:. "DON'T FORGET TO PUT THE NUT AND SLEEVE ON BEFORE BEFORE BEFORE YOU FLARE THE TUBE END."
Bob
Re: loader build resumes!
Posted: Sun Jun 26, 2022 11:09 am
by thebuildist
I'll post a few pictures later today, but IT'S COMING TO LIFE.
My hard lines/hoses plan went straight out the window, though.
I had originally intended to permanently mount the spool valve on the right fender and pipe four 3/8" hard lines from the work ports down to 4 quick disconnects under the right hand foot rest. From the disconnects I planned to run four long 3/8" hoses up the vertical receiver frame to 4 tees and then pipe from those tees out to the various cylinders. I bought the lines and hoses and fittings to make that happen.
But I've changed the location and setup of the new spool valve, having now mounted it permanently to the loader structure. So when I detatch the loader the spool valve will stay on the loader. So now there are only 2 quick disconnects, one for supply and one for return. And the spool valve is more unobtrusive with the loader attached, and of course completely disappears with the loader detached. Way better deal.
But it changes my hose/line routing, and unless I want to buy a bunch of new hoses and such, then I need to make it work with what I have.
So: I'll come out of my spool valve with 4 long hoses. I'm routing them down the inside face of the right hand boom arm and then out to four tees located in the center of the boom center brace. (The crossmember behind the bucket.) From there I'll pipe outward to the various cylinder ports. One benefit of this approach is that the fluid path length will be identical from side to side. Since I'm not installing proportioning valves between the two sides, it seems intuitive to me that this will help keeps the opposing cylinders in sync. It may not matter, I don't really know. But it can't hurt, and if I'm going to make use of those hoses, then that's what I need to do.
So I have the first two hoses run and piped into the boom lift cylinders. So naturally, I backed the tractor out of the basement workshop and started it up to see what would happen.
And the laws of physics are still in effect, so the boom went up and down on command! First time ever. Well, mostly. I had the work ports reversed for the hoses, so it went down when I told it "up" and vise-versa. But that was easily corrected.
Next I pipe in the two bucket cylinders. But I'm two swivel fittings short, so I may have to finish those up tomorrow after a trip to the hydraulics shop. The anticipation is KILLING me!
Bob
Re: loader build resumes!
Posted: Sun Jun 26, 2022 12:25 pm
by Eugen
Sounds like great progress Bob, looking forward to some pics. But even more so to see it ALIVE!!!

Re: loader build resumes!
Posted: Mon Jun 27, 2022 7:51 pm
by thebuildist
Well, the hoses are a bit of a mess. They're about 3 inches longer than they need to be, and it's surprising how tricky it is to tuck away an extra 3 inches of hose length.
I had to make several fittings on the lathe, a few because I didn't want to wait for or spend the time/money to go to the hyrdraulics shop. And a few because they're so unusual, I'm not sure anyone sells them.
Why do I need adapter fittings that are so unusual? It's like this: A while back I was looking on Ebay for hoses, and I sorted them by price. And the CHEAPEST hoses on Ebay that day were 3/8" hoses, 60" long. Parker branded, with some kind of swivel on one end, some other kind of mystery fitting on the other end. $7 each plus $11 combined shipping. So I bought 4 of them for $39 delivered.
I knew that I was going to have to buy some kind of adapters to make them work, and that only after I figured out what kind of fitting they were.
So they turned out to be #8 SAE Oring on the swivel end, and 18mm male cone fittings on the other end.
The SAE8 screwed right into my new spool valve, so that's awesome. But then I needed to adapt from 18mm male cone to JIC 6 male. So I created some 18mm female cone to JIC 6 female adapters. Problem solved.
But it was a PAIN making those metric cone fittings. I made a reamer to try to produce the female cone area consistently, but the low grade steel bar I'm working with kept galling on the reamer edge, so I'd have to cut off a few millimeters and ream it again, trial and error until I got a clean/smooth cut.
Maybe I should have just adjusted the lathe's compound and bored the cone/bevel shape. Who knows. But it's done now.
Anyway, having created a total of 8 custom fittings, combined with a whole slew of purchased fittings, and having made up 6 segments of 3/8" hard line, I finally was able to screw everything together. There were no leaks, unless you count that one JIC6 fitting that I forgot to tighten. That one leaked pretty hard!
But I didn't care for how the whole rat's nest looked. A big jumbled mess of hoses, that looked awful and are just begging to get snagged and damaged.
So I stood there for about an hour playing games with hoses, trying different routings until I was more or less happy with what I had.
It's not TOO terrible as it is, and I'm going to add a piece of 6" steel channel in front of the hoses, which will conceal the ugly nest, and provide some protection. But for this second, it's good enough.
And finally: video evidence that it all works as advertised:
https://youtu.be/Al6tqy3_kSs
Bob
Re: loader build resumes!
Posted: Mon Jun 27, 2022 9:08 pm
by Spike188
Very smooth. I am impressed.
Re: loader build resumes!
Posted: Mon Jun 27, 2022 9:12 pm
by DavidBarkey
Re: loader build resumes!
Posted: Mon Jun 27, 2022 9:43 pm
by Eugen
Yay!! Moves very nicely Bob, you're unstoppable, you've done it! Great job!
Re: loader build resumes!
Posted: Mon Jun 27, 2022 10:43 pm
by JSinMO
That is awesome!
Re: loader build resumes!
Posted: Tue Jun 28, 2022 7:45 am
by Harry
Congratulations Bob. The feeling of accomplishment is terrific.
Keep the Peace
Harry
Re: loader build resumes!
Posted: Tue Jun 28, 2022 9:30 am
by Chad
Congrats Bob! A long time coming but well worth it from the looks of it. Well done!
Sent from my Pixel 4a using Tapatalk
Re: loader build resumes!
Posted: Tue Jun 28, 2022 10:53 am
by MattA
Nice work Bob

Re: loader build resumes!
Posted: Wed Jul 13, 2022 11:01 am
by thebuildist
A little cleanup and detailing this morning:
I built a lightweight aluminum cover to conceal the rat's nest of hoses and help to keep them routed and organized.
I created a "conduit" on top of the right hand boom arm to contain and dress up the hoses down that path. It's 2" gray PVC conduit, sliced longitudinally, and clamped to steel straps that I welded to the top of the arm.
While I was at it, I re-routed the hoses a bit to clean up their appearance and minimize hose strain.
I painted the 3 exposed pressure and return pipes, which are raw steel and will rust very quickly.
I clamped the pressure supply pipe to the diagonal brace in order to transmit its vibration/handling strain to that diagonal brace.
I created a bracket to which I clamped the return pipe as it enters the tower. This transmits the return pipe's vibration/handling strain into the bracket, which is bolted straight to the tower. Without that bracket, all that stress and strain was hanging on the hydro filter housing, which is a soft zinc or magnesium and not nearly strong enough for that load.
The pipe coming out of the loader valve was kind of hanging in free space, so I clamped its far end to the loader structure, since that end is where the strain of handling happens. Without a clamp there, the torque applied by vibration and handling will eventually loosen up the joints of that pipe as it runs over underneath the loader valve.
Final steps:
Bucket modifications and mounting and
Calculating and creating the concrete counterweight.
Re: loader build resumes!
Posted: Wed Jul 13, 2022 6:18 pm
by Timj
Re: loader build resumes!
Posted: Sun Jul 17, 2022 2:16 pm
by thebuildist
After the Bad Day From Heck, I'm recovering nicely.
BTW: not to dwell on it, but I found out the next morning that a limb had fallen on my golf cart, destroying its canopy/roof. It was just not my day.
Anyway, recovering and resuming meant torching out the angled section that I need to remove. With that gone, I was able to put the bucket in the shop press and bend the flap outward that I had previously bent inward, putting it back more-or-less where it belongs.
That left me with a big sheet of steel with a crease in the middle, and I needed that crease to be gone. So I just worked my way down the length of the bend, bringing the ram down every 2 or 3 inches, pressing it flat as I went. This is time-consuming on an electric press since I had to bring the ram down 50 or more times. And it's and basically impossible on a manual press. There's no reason it couldn't actually be done, but a normal person just wouldn't have the willpower to stand there pumping the handle thousands of times all day long. It's just too demoralizing.
But with the electrified press it only took about 30 minutes to make a total of 3 passes , hopping a couple inches each time, up and down the crease and the now bowed centerline of the two "flaps". Ultimately it left the steel sheet fairly close to flat.
For those who might find it interesting, I electrified the press myself, using an old airless paint sprayer as the hydraulic pump. Details here:
https://www.youtube.com/watch?v=TJJYvZ8D5YI
Then I trimmed the sheet to size and welded it into the gap.
The steel is around 1/8", and I used 3/32 7014 welding rod, which works very nicely. Not as clean and perfect as MIG, but not bad at all.
That left two sets of big gaps to be filled: The large open triangles where the flat plate transitions out to the original protruding/angled profile of the bucket shell, and the small diamond shaped cutouts left behind where I mistakenly cut the bucket shell the first time.
I used cardstock to make a template for the shapes I needed, then trace that shape onto steel place using a carbide scriber, then cut it out on the bandsaw.
Again welded with 3/32 7014 rod
So now I'm finally back to where I thought I was on Thursday, ready to attach the bucket shell to the quick-attach adapter.
But for the first time, I get to see what the machine will actually look like once it's finished up. And I'm liking what I see!
Bob
Re: loader build resumes!
Posted: Wed Jul 20, 2022 9:19 pm
by thebuildist
We're in the home stretch!
As of yesterday, the bucket is mounted. Not much to tell, I finished off in the direction I started. This time I flattened out the correct protrusion and ran a whole lot of weld bead.
Then ran a couple pieces of 4"x1/4" angle iron vertically at the back corners to carry the twisting forces up to the top of the bucket, because the quick-attach plate itself is mounted pretty low.
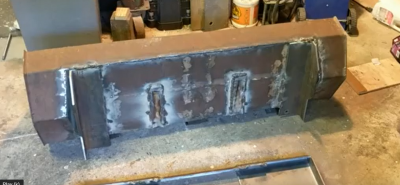
Then I drove the tractor up on 1.5" high boards, put the bucket flat on the floor, snugged the bucket up tight against the quick-attach plate, and tack welded it in place. I'll be welding a 1/2" hardened cutting edge underneath the current cutting edge. That extra 1/2" depth, combined with the tractor being 1.5" up in the air will give the bucket a 2" below grade cutting level. At full height it sits at 5'8" when it's level. I'm slightly underwhelmed by that figure, I had hoped to lift higher than the 5'11" of a stock 644. But all things told I chose the geometry I did for the best sense of strength and safety and good judgement. So I can live with it. If I built a second loader, I could start with this exact object and improve it. But working from a set of drawings created by nothing but my imagination, I'm still pleased with it.
Having said all that, it's not quite true to say "it's mounted." It's wasn't fully mounted, because the quick-attach bracket on the tractor didn't yet have locking pins installed. So if you back-dragged with it, the bucket would come off. That would be inconvenient.
So today I built and created the quick-attach locking pins.
I wanted a hardened pin, so I cut up the super hard shaft of a chisel from an electric jackhammer. I welded that pin to some 1" threaded rod. The idea is that turning the threaded rod will cause the pin to extend and retract.
I wanted the pin to have a large surface to bear against, so I drilled a matching hole through some 1" steel plate.
Then I used a piece of 1" black pipe as a spacer and welded the plate, spacer and 1" nut into a single assembly. Then I threaded/spun in the pin and welded a cheap socket on the end of the threaded rod, so that a 3/8 square driver can turn it.
Then I took some 7/16" rod and bent it into a speed handle. I ground a 3/8 square on one end, and now it's the driver tool to spin the pins in and out.
Finally I welded the pin assemblies in place. While I had the welder and tools out, I went ahead and welded some tabs and a spring in place on the back side of the quick-attach bracket, and that provides a way to mount the speed handle for storage. So though it's not great to have to use a tool to change quick-attach implements, at least that tool is permanently attached near where you need it.
So I'm down to 3 items: Weld on the new cutting edge, paint the bucket, and build a concrete counterweight.
Bob
Re: loader build resumes!
Posted: Wed Jul 20, 2022 11:32 pm
by Eugen
I would not be bothered by the 5'8" lifting height. It sounds good the higher the better, but if you went much higher, it would no longer be proportionate to the length of your tractor. If you really wanted to lift things much higher, perhaps you can make yourself a quick attach boom of sorts.
It's not easy to understand the quick attach mechanism you have now, but it seems good. Something I would definitely like to have on the 644.
Re: loader build resumes!
Posted: Thu Jul 21, 2022 1:11 pm
by thebuildist
I didn't want to reinvent the wheel, so I researched what quick-attach is out there. I decided that the "universal" skidsteer quick-attach system is too large for this machine and unnecessarily complicated and expensive.
I came across the quick-attach used by Toro Dingo and that seemed like a good approach.
It's a lot like the "french cleat" used to hang cabinets on a wall. The implement has a folded over upper lip/cleat, and the machine has an adapter/platen that slips up under the cleat and lifts it up. Upon lifting, the implement rotates down and flattens back against the platen of the adapter, where it is then locked in place by two pins.
I would like to have used it in its stock configuration. But I really wanted the lifting point of the platen/adapter to be as wide as the boom. So I chose to use the Toro system, but make it wider, more like 29 inches wide instead of only 18 inches wide.
To make the permanent tractor quick attach assembly, I cut a "hooking" shape into each of the shackles that form the two bucket rotation joints at the bottom of each boom arm. And I then joined those two shackels by 6" C-channel, effectively making them into a single unit. That hook shape slips up under the lip/cleat of the bucket adapter plate. And then bought a couple of off-the shelf Toro Dingo bucket adapter plates and split them down the middle.
I hope this makes sense...
Bob
Re: loader build resumes!
Posted: Thu Jul 21, 2022 1:22 pm
by Eugen
Now it's clear, thank you for this!
Re: loader build resumes!
Posted: Fri Jul 22, 2022 3:04 pm
by thebuildist
Looks like I can check my bucket off of my bucket list...
Bob
Re: loader build resumes!
Posted: Fri Jul 22, 2022 3:38 pm
by Eugen
Quite amazing how fast you get things done once you delve into it! Very nice! I think you have so far the best diy loader for a garden tractor that I've seen anywhere on the web. Congrats Bob, you're going to be star among us tractor nuts!

Re: loader build resumes!
Posted: Fri Jul 22, 2022 4:45 pm
by thebuildist
Thank you, Eugen!
I think that's the nicest thing anyone has ever said to me!
Bob
Re: loader build resumes!
Posted: Fri Jul 22, 2022 5:34 pm
by JSinMO
Eugen wrote: ↑Fri Jul 22, 2022 3:38 pm
Quite amazing how fast you get things done once you delve into it! Very nice! I think you have so far the best diy loader for a garden tractor that I've seen anywhere on the web. Congrats Bob, you're going to be star among us tractor nuts!
I agree!! Can’t wait to see pictures of your creation at work!
Re: loader build resumes!
Posted: Sat Jul 23, 2022 9:04 am
by thebuildist
Today I calculate and create the counterweight.
But here's a look at how the quick-attach works.
https://youtu.be/dJcoP_i3bfo
One big job in front of me is figuring out how to compile the hydraulic build process into a coherent video. Up to this point I've simply filmed as I went and assembled the first 4 videos within a week or two of their actual work. It was very straightforward.
But the hydraulic process began (and failed) back in... October? And as everyone here knows, it has come through multiple attempts and iterations before it succeeded. I'm undecided as to how to portray that in a video.
I've been making the videos to provide to the average person an overview of the journey. Not really a "howto" but more like, "If you wanted to try this yourself, here's the kinds of things you'll encounter along the way." And that applies for any kind of garden tractor. But for the hydraulic phase of the work, what I experienced really only applies to Case/Ingersoll machines, and PS models in particular.
So I'm thinking that video 5 will be more of a "guided tour" than a "watch me work" kind of video.
Anyway, I've got to get that figured out next.
But not today. Today I "make counterweight while the sun shines."
Bob
Re: loader build resumes!
Posted: Sat Jul 23, 2022 6:12 pm
by thebuildist
Well, I was surprised. And a little puzzled. But I think I have it licked.
I bought 11 bags, 60 lbs each of concrete. I figured I'd need more or less 500 lbs to build the counterweight, and I'd use the rest on a slab I need to pour.
The slab pour is waiting on the loader, oddly enough.
I figured the tipping point would be around 400 lbs, which is to say, "With 400 lbs at the lip of the bucket, the back wheels will come up in the air."
So I loaded up 8 bags. And the bucket came up, and the back wheels didn't.
So I loaded all 11 bags. Same thing.
So I scrounged around and found a 20lb bag of lime, a 40 lb bag of mortar mix, and what turned out to be 80 lbs of cast steel bucket teeth, and stacked all of them on top of the concrete. precisely 799 lbs.
And the bucket came up, and the back wheels didn't.
So I got off the machine and walked around back and lifted up on the 3pt bar. And with my official guesstimate of 65lbs of lift, the back wheels stubbornly rose into the air.
So I'm using that figure.
Some long calculation later, I came to this conclusion: "To keep 400lbs downforce on the back wheels while carrying 1000lbs at the lip of the bucket, I need a 621 lb. counterweight hanging from the 3pt. lift arms."
Concrete weighs 150lbs per cubic feet, so I need a 4.15 cubic foot counterweight.
Like so:
Opinion question: This is larger than I had anticipated, and I've thought about making it the same footprint size, but only... 18" high instead of 24.5". That would give me the option to try out the performance of a smaller weight first, but leave me the option to add another 6" of height to it later if I need to.
What is everyone's advice? Make it full size the first go-around, or make it a little smaller and see how it does?
Bob
Re: loader build resumes!
Posted: Sat Jul 23, 2022 6:53 pm
by Timj
I don't think there is an answer in here, maybe more questions, maybe I'm just thinking out loud.
Would there be a benefit to you to have a two piece counterweight? Less weight for average use, and an add on for when you get serious.
Pro- less weight on tractor when not needed
Con- may be a bigger pia than it's worth handling the add on piece?
Another thought that I think applies is the change in tractor balance when turning sharp. I don't know if those with the 64x tractors notice this or not. I really notice it on our compact tractor when using the loader. I've been going to add more weight to the rear and see if helps. I get so use to running the full size TLB that's pretty planted to the ground, I've had a few hair raising experiences when I get zooming around with that smaller, short wheel base tractor.

Tim
Re: loader build resumes!
Posted: Sat Jul 23, 2022 7:56 pm
by JSinMO
I think Tim’s idea of a 2 piece counterweight has good merit and should be considered. I know that there is a weight and balance point difference from your tractor to the 648, but I can tell you with a fixed rear weight of 800 LBS in the backhoe the front wheels could easily spend more time off the ground than on it when driving with nothing in the bucket even with the 500 LBS counterweight under the front. I almost never put the tractor in high gear for that reason.
I really have to watch it even in low gear the front will really float on rough ground or inclines.
So to me the question is how often will there be 1000LBS on the edge of the bucket? As opposed to a lighter weight filling the bucket. I think you will really notice that 600 LBS weight back there when your just moving around with no load or light to average loads in the bucket.
I would think a 2 piece weigh design would help this.
In my case I have started to think about taking the backhoe off the tractor when I don’t need it so the tractor is more stable.
Re: loader build resumes!
Posted: Sat Jul 23, 2022 10:52 pm
by thebuildist
I appreciate the feedback, and that's kind of the same way I'm thinking. I hadn't really thought of an official two-piece design, and that's a great idea. A smaller weight for general work, the full monty for heavy work. I did have a sense that I might not enjoy all 600lbs following me around every time I need the loader for anything.
I think I'll look at it with an eye towards easy handling: a way that I can have multiple counterweight options without hurting my back.
It might be that I just build two different weights, a big one and a little one. But I'll do some figuring and thinking along those lines.
Thank you, gentlemen!
Bob
Re: loader build resumes!
Posted: Sun Jul 24, 2022 8:16 am
by Eugen
I currently have 104 lbs on each rear wheel of the 644 and about six 40 lbs suit case weights in the rear box. Me in the seat another 140 lbs or so. Carried full buckets of sand, gravel, and large ash logs and never felt like more weight at the back would help. Another advantage of multiple smaller weights is that you may try one size and find you don't need more. @DavidBarkey made some great wheel weights out of concrete and he documented that in a thread here. IMHO wheel weights should be a priority as it does not add weight to the axle and most likely you never have to take them off. Just my 2c
Re: loader build resumes!
Posted: Sun Jul 24, 2022 8:47 am
by DavidBarkey
Bob , I have run a home loader on Frankie for many years now . I can tell you from experience that splitting the counter weight is key and distance is your friend .
Rear wheels are loaded , now I spent the money on the special tubes and had professionally filled with calcium . They weight 300lbs each . plus bolt on weights
The counter weight I use is off the back of the 3 pt hitch 3 bags of create in 2 5 gallon pails = 180 lbs but distance off the back make it do more for less .
By splitting where you put the weight you split the forces on the axles . With strictly chassis weight , when ever you are unloaded all that weight is on the rear axles . By splitting the weight you reduce that . When loaded the the forces of weighted wheel will be pulling down on the axles while the chassis weight will be pushing down on the axle housing . If done correctly they cancel each other out reducing the load on the axles and housing .
Now there are many ways to achieve wheel weight and chassis weight . This is what I have done .
Now all that loader weight will be on that front axle . Sorry , can't remember what did you to to address that . ?
Re: loader build resumes!
Posted: Sun Jul 24, 2022 10:42 am
by JSinMO
@Eugen and
@DavidBarkey
Have good points putting the weight on the axels.
If you look at my 830 ( I know not a garden tractor, but the concept it the same ) I’ve never run extra weight on the back of the tractor. All my counterweight is at the axels.
I have tires filled with calcium chloride, 2 sets of weights and the iron hubs for duels and that’s it. I’ve never felt like I needed more weight on the back.
Calcium chloride works well, but when it eventually leaks it can destroy you rims over time and make a mess. I know some people have used beet juice, or windshield washer fluid in there tires as a replacement. If you go that route you want something that won’t freeze.
Re: loader build resumes!
Posted: Sun Jul 24, 2022 11:05 am
by thebuildist
DavidBarkey wrote: ↑Sun Jul 24, 2022 8:47 am
Bob , I have run a home loader on Frankie for many years now . I can tell you from experience that splitting the counter weight is key and distance is your friend .
Rear wheels are loaded , now I spent the money on the special tubes and had professionally filled with calcium . They weight 300lbs each . plus bolt on weights
The counter weight I use is off the back of the 3 pt hitch 3 bags of create in 2 5 gallon pails = 180 lbs but distance off the back make it do more for less .
20211010_143154.jpg
By splitting where you put the weight you split the forces on the axles . With strictly chassis weight , when ever you are unloaded all that weight is on the rear axles . By splitting the weight you reduce that . When loaded the the forces of weighted wheel will be pulling down on the axles while the chassis weight will be pushing down on the axle housing . If done correctly they cancel each other out reducing the load on the axles and housing .
Now there are many ways to achieve wheel weight and chassis weight . This is what I have done .
Now all that loader weight will be on that front axle . Sorry , can't remember what did you to to address that . ?
I won't have my weight split left to right, but it will be slung 24" behind the rear axle, 6 feet behind the front axle. So that's decent leverage.
One of my design goals is to have the tractor "100%" usable as a normal lawnmower. The loader will only be used occasionally, so I want to make the transition from "mower" to "loader" quick and painless. I have the rear tires loaded with RV antifreeze, and the vertical receiver shackles will remain installed on the machine all the time. So those changes are "permanent". But the loader assembly and valve will come completely off (in 3 to 5 minutes) and I'd like my counterweight to be similar. That's why I'm planning to use a big single weight slung from the 3 pt. I can back up to the weight, pin the 3pt arms onto the counterweight's steel lugs, and drive away, ready for loader duty.
I think the most "painful" part of loader transition will be installing a set of 2-link tire chains. I figure I'll need those any time I'm doing wet/muddy work for sure. But not if I just need to move something heavy, etc.
I say all that to say that I at least want to try going down this road of a quick/easy/removable concrete counterweight on the 3-pt. But I know full-well that it may not work out like I envision.
As for the front axle, that was the very first thing I addressed, building a new heavy duty front axle with timken bearing hubs. It all on my youtube channel for anyone who's curious.
Bob
Re: loader build resumes!
Posted: Sun Jul 24, 2022 12:47 pm
by DavidBarkey
@thebuildist Bob , a good point about it being a lawn mower for the most of the time . Mine is a full time tractor , never a mower . The one of the down sides to extra is trying to stop it . I had to put disk breaks on mine . Ya if you are not running lugs which a not good for mowing chains will be a must . Yes they can be a pain to in stall on loaded tires . How much weight did you get out of the RV fluid ?
Re: loader build resumes!
Posted: Sun Jul 24, 2022 1:59 pm
by thebuildist
This has been on my mind all night, and I've figured it out.
How can it be that I need such an expectedly large counterweight while at the same time the bucket was able to lift way more than expected without any counterweight? Those two things are in conflict.
So I've gone back through my mental process, and found a glaring logic error. It turns out I don't need nearly as large a counterweight as I said yesterday.
What I did was find the balance/tipping point, the amount of weight the bucket can lift before the back wheels come off the ground. It turns out to be very near 1000 lbs. (799 in the bucket, 36 inches from the front axle, plus 65 lbs lifting, 72 inches from the axle. 65lbs at 72 inches is equal to 195 lbs at 36 inches, so the tipping point is right around 994 lbs in the bucket.)
Then I calculated the torque effect of 994 lbs in the bucket and mentally said, "The weight on the rear needs to counteract that torque effect." and started figuring from there. But that's a false assumption: It takes 994 lbs in the bucket to achieve equilibrium. With 994 in the bucket, both sides are zero.
So the counterweight doesn't need to offset "zero plus 994". It only needs to offset "zero", plus add 500lbs to the rear axle. And the operator's weight helps as well.
I was actually calculating the counterweight that would be needed for TWO thousand lbs in the bucket, rather than ONE. Duh.
So 310 lbs will be plenty. Since my concrete is in 60 lb bags, I'll just mix up 5 bags and call it good.
So no messing around with big counterweights and little ones. A single 300 lb counterweight will be just fine for all purposes.
And I'm relieved.
Bob
Re: loader build resumes!
Posted: Sun Jul 24, 2022 3:00 pm
by Timj
Nice catch Bob, when the gears keep turning sometimes we get lucky and catch things before we start.

it seemed like alot of weight, but I didn't really have a good comparison.
So my question is " did you sleep at all last night"?

Re: loader build resumes!
Posted: Sun Jul 24, 2022 4:31 pm
by thebuildist
Timj wrote: ↑Sun Jul 24, 2022 3:00 pm
Nice catch Bob, when the gears keep turning sometimes we get lucky and catch things before we start.

it seemed like alot of weight, but I didn't really have a good comparison.
So my question is " did you sleep at all last night"?
One thing I don't fool around with is sleep! Time for bed is just that!
And I have a reminder/helper....
Bob
Re: loader build resumes!
Posted: Sun Jul 24, 2022 4:49 pm
by DavidBarkey
It is a good thing you are smart at that fancy math Bob
@thebuildist I admire your abilities . I wanted to be a mechanical engineer when I was young , but was not good enough in school . Oh well I muddle through in my own way . lol If I tried to do the kind of math you are talking about , I would blow another gasket before I got the answer right . Me I did it the red neck way . Built the loader and then tried to pick something up . All I did was pick the rear wheels (apparently I am not enough counter balance ) . So had the tires loaded . Well that was better , but still not enough . So how much more do I need ? Start hanging weight off the 3 pt. untill reached a desired result . turned out to be about 200lbs in my case . 3 x 60lbs plus steel frame . Close enough .

Re: loader build resumes!
Posted: Sun Jul 24, 2022 6:53 pm
by thebuildist
Yours is the only way that always works!
I really appreciate your kind words. I just really enjoy playing with this kind of stuff, figuring out the puzzles, overcoming the challenges along the way. It's how I unwind.
I'm really blessed to have a lot of good things in my life, including the time and health to get to do stuff like this.
Bob
Re: loader build resumes!
Posted: Mon Jul 25, 2022 2:43 pm
by thebuildist
DavidBarkey wrote: ↑Sun Jul 24, 2022 12:47 pm
@thebuildist Bob , a good point about it being a lawn mower for the most of the time . Mine is a full time tractor , never a mower . The one of the down sides to extra is trying to stop it . I had to put disk breaks on mine . Ya if you are not running lugs which a not good for mowing chains will be a must . Yes they can be a pain to in stall on loaded tires . How much weight did you get out of the RV fluid ?
It added 118 lbs per tire.
And I already own the necessary brake drums. And some calipers that I think will work. And a couple of brake master cylinder assemblies.
So... I'm thinking independent disk brakes are in my future. But it could be a while. I haven't yet figured out the geometry for where to put the master cylinders and how the split pedals will drive them. But I'm thinking about it.
Meanwhile, here's my fancy counterweight being constructed:
I made a single re-bar ring and hung it from the main steel through-shaft, about 1" off the bottom, so that the steel rebar is providing the "lift" for the weight of the concrete. I cant imagine it matters at all in the near term, but 20 years from now it could keep the thing more together.
Bob
Re: loader build resumes!
Posted: Mon Jul 25, 2022 5:04 pm
by Eugen
Are you not worried it'll split further down the road? I see you're not using any steel mesh for reinforcement.
Re: loader build resumes!
Posted: Mon Jul 25, 2022 5:54 pm
by Jancoe
Eugen wrote:Are you not worried it'll split further down the road? I see you're not using any steel mesh for reinforcement.
Was thinking the same too. I busted up a fireplace hearth at my old house that had probably 20 ft of chicken wire in it. What a pain that was to bust up.
Sent from my SM-G975U using Tapatalk
Re: loader build resumes!
Posted: Mon Jul 25, 2022 9:12 pm
by thebuildist
Well, I THOUGHT about mesh wire. But the thing is that it literally does nothing but hang around. No impacts, no pressure, etc. So I figure the only stress it will have is the tension of hanging from the crossbar. And that's what the rebar I did put in is for.
You may actually be right in the end. But I don't see any reason it shouldn't hold together.
Bob
Re: loader build resumes!
Posted: Mon Jul 25, 2022 9:29 pm
by DavidBarkey
Eugen wrote: ↑Mon Jul 25, 2022 5:04 pm
Are you not worried it'll split further down the road? I see you're not using any steel mesh for reinforcement.
I have had those 2 concreate weight hanging off a 1" bar with a horse shoe shaped rebar weld it to it to keep from spinning on it . No cracking here , and I have forgot to lift it many of times before moving tractor . What Bob has done will hold just fine . imo.
Re: loader build resumes!
Posted: Mon Jul 25, 2022 9:31 pm
by Spike188
I will agree with Bob. His design has the concrete setting on the rebar. If the concrete was suspended by pins in the top then mesh might be best. Concrete is strongest in compression mode.
Re: loader build resumes!
Posted: Thu Jul 28, 2022 8:30 pm
by thebuildist
The counterweight has now set up for 72 hours. It won't reach full strength for several more weeks. But at this point it ought to be at 70% of its eventual strength.
So after exercising extreme patience by waiting for 3 whole days, tomorrow I will drill out the pins for the three-point lift arms, and weld on some kind of ears for the top link to engage in. And pick up the new counterweight for the first time!
Then I'll undoubtedly drive around here looking to pick a fight with the first heavy thing I can find!

Re: loader build resumes!
Posted: Thu Jul 28, 2022 8:35 pm
by thebuildist
By the way, I know everyone is probably bored to tears of this topic, but one last detail: I went ahead and removed the loader a couple evenings ago so that I could keep the tractor locked up well I was not actively working on it from day to day.
And it took almost exactly 5 minutes to remove. And would have taken less, except that my steel saw horse turns out to be a little bit too short with the handles of the loader valve sticking up in the air. So the next morning I added some leg extensions to the sawhorse and got its main bar moved up higher. So in its final form I think I can expect it to take about 4 to 4 and 1/2 minutes to install or remove the loader from the machine.
Which I am very pleased with.
Re: loader build resumes!
Posted: Thu Jul 28, 2022 10:19 pm
by JSinMO
I’ve enjoyed this series, even though your technical knowledge surpasses mine by quite a bit! Very impressive work. If I can make a request I’d like to see a video of the loader being attached / disconnected.
Re: loader build resumes!
Posted: Fri Jul 29, 2022 6:08 am
by thebuildist
I'd be happy to. Next time I install it I'll film it.
Bob
Re: loader build resumes!
Posted: Fri Jul 29, 2022 9:38 am
by Eugen
Not bored at all Bob, it's really for me at least to see what other people face do and what you do is quite unique for sure! So, post as you feel!

Re: loader build resumes!
Posted: Sun Jul 31, 2022 1:16 am
by thebuildist
Ok here is a video from a couple days ago taking the loader off.
https://www.youtube.com/watch?v=0wUvcjJSEy0
And one from this morning doing the install.
https://www.youtube.com/watch?v=xvSOfV6VpDI
Bob
Re: loader build resumes!
Posted: Sun Jul 31, 2022 8:27 am
by Spike188
Well done Bob. Very smooth system.
Re: loader build resumes!
Posted: Sun Jul 31, 2022 9:47 am
by thebuildist
Thank you, Spike!
Bob