Page 1 of 1
Converting the AC stick welder to DC
Posted: Mon Oct 24, 2022 12:34 pm
by Eugen
Like I needed another project. Yet, for a few reasons I am taking a stab at converting the AC stick welder to DC. For one, the latest welds I did on the 644 with the AC welder, using 6011 electrodes, were pretty ugly. I'm pretty sure it's not the welder's fault, but mine, lacking technique. Still, I feel that it would be nice to switch the welder to DC.
As I said, I already have a rectifier bridge apparently capable of doing 400A and up to 1600V. I take that with a big grain of salt. The size of the device is about 3.5x2.5 inches, and maybe 3/4 inches thick. Looking at some data sheet found on the internet for this China made device, the power dissipation vs mean current:
Gotta love the lack of numbers on the graph. I'm assuming each line is 100 amps on the x axis, and 100 watts on the y axis. I doubt I'd weld at 200 amps, but let's just pretend I do. According to the graph the power dissipation would be a little less than 200 watts. To dissipate 200 watts you need a pretty good size heat sink, and air flow. There isn't enough room in the case of the welder for a proper size heat sink. I could use a heatsink on the outside of the case with a 12V fan attached to it, but that just complicates everything. More thinking

needed.
Re: Converting the AC stick welder to DC
Posted: Mon Oct 24, 2022 3:53 pm
by FUTZ
200 Watts does seem too much, less than 1/3 HP. Motors that size don't have fans. And, unless you're working on a pipeline, you won't be welding too long. Put the biggest heat sink you have, and give it a try, see how hot it gets. I think I have some aluminum extrusion somewhere.
Re: Converting the AC stick welder to DC
Posted: Mon Oct 24, 2022 4:05 pm
by thebuildist
I have some pretty big aluminum heat sinks, about 8 in wide by 12 in long. You're welcome to have one if you want to pay shipping.
Re: Converting the AC stick welder to DC
Posted: Mon Oct 24, 2022 4:20 pm
by Eugen
FUTZ wrote: ↑Mon Oct 24, 2022 3:53 pm
200 Watts does seem too much, less than 1/3 HP. Motors that size don't have fans. And, unless you're working on a pipeline, you won't be welding too long. Put the biggest heat sink you have, and give it a try, see how hot it gets. I think I have some aluminum extrusion somewhere.
Thanks, I got some heat sinks, I'll see what fits. Just pulled off the fan cover which was taking a lot of room. Will post pictures soon.
200 watts may not be much, but the max junction temperature is 150C and solid state devices have a very sharp fry turning point. I'll test it with what I have and if not good enough I'll try with a bigger heat sink.
I had certain fun making 4 awg cable lugs from 1/2" copper pipe. Found a transformer with a thick secondary to use as output choke, but it needs a core gap so I wasn't looking forward to cut a gap in the core.

Re: Converting the AC stick welder to DC
Posted: Mon Oct 24, 2022 5:55 pm
by thebuildist
That's why you need a metal cutting band saw.
But a narrow cutting disc in an angle grinder will do the trick.
Re: Converting the AC stick welder to DC
Posted: Mon Oct 24, 2022 11:36 pm
by Eugen
Well now, my welding technique still sucks but now it sucks DC
This is what I cobbled up
Re: Converting the AC stick welder to DC
Posted: Mon Oct 24, 2022 11:47 pm
by Eugen
I am amazed how well it works. And the heat sink doesn’t even get warm to touch on 110 amps and continuous welding for a couple of 1/8 6011.
Re: Converting the AC stick welder to DC
Posted: Mon Oct 24, 2022 11:52 pm
by Spike188
In the second picture is a transformer sitting on the floor. Is that the choke? Is it connected only to the primary side and open on the secondary side?
Re: Converting the AC stick welder to DC
Posted: Tue Oct 25, 2022 12:05 am
by Eugen
Spike188 wrote: ↑Mon Oct 24, 2022 11:52 pm
In the second picture is a transformer sitting on the floor. Is that the choke? Is it connected only to the primary side and open on the secondary side?
Yes, except it's connected only on the secondary. This is not finished, I want to take it out and gap the core, and add thermal paste between the heat sink and diode bridge.
Re: Converting the AC stick welder to DC
Posted: Tue Oct 25, 2022 8:27 am
by thebuildist
wait 'till you try 7018 on DC. You'll feel like you just graduated welding school.
The difference between 6011 and 7018 is amazing.
Bob
Re: Converting the AC stick welder to DC
Posted: Tue Oct 25, 2022 9:44 am
by Jancoe
Your right about 7018. It produces a very smooth weld without all that spatter. Absolutely nothing like 6010 or 6011. Welding with a DC stick over an AC unit on steel will run smoother any day. I bought a cheap ebay "accurate tools brand" 3 in 1 DC inverter welder. Stick, tig and plasma a few years ago and has done everything I need. Had to take it on a road trip and do some welding up on some poles for a business sign.
Sent from my SM-S906U using Tapatalk
Re: Converting the AC stick welder to DC
Posted: Tue Oct 25, 2022 9:58 am
by Eugen
thebuildist wrote: ↑Tue Oct 25, 2022 8:27 am
wait 'till you try 7018 on DC. You'll feel like you just graduated welding school.
The difference between 6011 and 7018 is amazing.
Bob
How do you store the 7018 so they don't go bad? I'd hate to use a few electrodes and throw out the rest.
Re: Converting the AC stick welder to DC
Posted: Tue Oct 25, 2022 11:35 am
by thebuildist
The storage thing is overblown. If you're doing certified/x-rayed pipeline and such I'm sure it matters. And then it's all about moisture content, so you have to basically bake them before use.
But for normal stuff it doesn't matter. My first batch came with my old welder, and were at least 10 years old, and they all worked fine. Now I buy them 10lbs at a time and store them on the shelf. Not even sealed. Those 10lbs will last me... a year or so? And I've never had any go bad.
Bob
Re: Converting the AC stick welder to DC
Posted: Tue Oct 25, 2022 11:54 am
by DavidBarkey
Eugen wrote: ↑Tue Oct 25, 2022 9:58 am
thebuildist wrote: ↑Tue Oct 25, 2022 8:27 am
wait 'till you try 7018 on DC. You'll feel like you just graduated welding school.
The difference between 6011 and 7018 is amazing.
Bob
How do you store the 7018 so they don't go bad? I'd hate to use a few electrodes and throw out the rest.
Just high and dry . If no where to store where reasonably dry then , when needed take twice what you think you need spread out on old baking sheet and bake in oven at 200 F for half an hour .
I keep a bunch of rod in a pipe hung just below the radiant tube heater year round with no issues .
Re: Converting the AC stick welder to DC
Posted: Tue Oct 25, 2022 11:58 am
by Eugen
You guys are great! I'll get some then

Re: Converting the AC stick welder to DC
Posted: Tue Oct 25, 2022 7:34 pm
by Timj
I think you'll be fine storing your rod in the plastic case 5 or 10lbs comes in. I keep mine in rod storage tubes with rubber gaskets, but I buy 50lbs at a time. It comes in a sealed metal can, like a big square soup can. Once I open it I need a way to protect the rod on the job so I just fill a bunch of the tubes.
Re: Converting the AC stick welder to DC
Posted: Wed Oct 26, 2022 8:42 am
by Harry
For keeping the E7018 electrodes dry I took an old electrical cabinet. Spot welded some short 1/4" round rods in it to hold shelves made from screening. I glued some foam on the inside of the box and installed a receptacle for a light bulb in the lower corner. The heat from the light bulb gives off enough heat to keep the flux dry. Every time I go to get some rods out of the box, which is not very often the light bulb is burnt out.
Keep the
Harry
Re: Converting the AC stick welder to DC
Posted: Wed Oct 26, 2022 3:01 pm
by Eugen
I was forced to take some vacation days because we're not allowed to accumulate too many, so after tiling the garden and doing some other stuff, rain started and the littlest one went for the afternoon nap. Took advantage of the situation and visited the local Linde (now Messer) gases and welding shop. Going to this store is like I'm a kid in the candy shop. Chatted to the guy there for about 15 minutes and he said if I wanted a quality 7018 that's easy to use he recommends the ESAB OK 55.00, some electrodes made in Sweden. I told him I don't want any stinking Ikea rods

just kidding, I said no such thing.
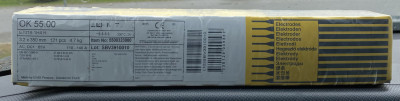
- ESAB OK 55.00 7018 welding rods.
Got the smallest package they had, 10 lbs, for about $63. These were not the cheapest rods, and that is just fine.
He also gave me advice about the MIG gun liner and about replacing my B tanks of acetylene. The service in this shop is exemplary, a pleasure to shop there.
Back to the AC welder conversion. Having it tested successfully, it was time to do things right. Got some thermal paste yesterday from work because I could not find mine anymore (it's here, but where?!?

). Thermal paste goes between heat sink and device, to facilitate heat transfer away from the device, to the heatsink, which then dissipates it into the air. The trick about thermal paste is to put very very little, just enough as to have no tiny air pockets between the two surfaces. The way I do it is I rub it onto the surface as thin as I can using a finger, and then I rub the two devices together gently as to spread it as evenly as possible. If any grinding is felt, I put a tiny bit more paste, then rub the devices again, until it feels like the two surfaces slide softly against each other.
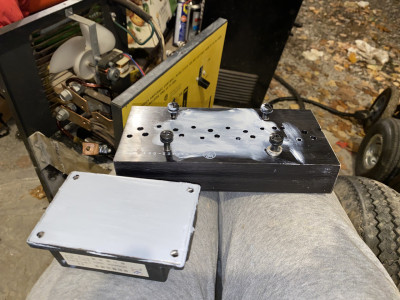
- Thermal paste rubbed on both surfaces.
After that, the device got bolted on the heat sink, and connected back in the circuit, making sure it clears the sides of the enclosure.
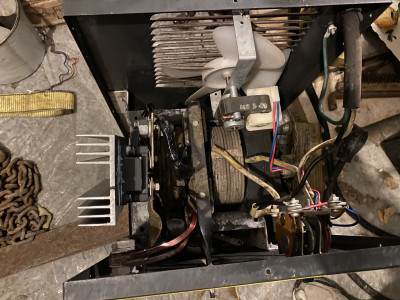
- View from above. Wanted to make sure it fits nicely within the case.
Re: Converting the AC stick welder to DC
Posted: Wed Oct 26, 2022 10:41 pm
by MattA
Good work Eugen. That fan might provide enough air flow in the chassis to keep your diode bridge cool. The black anodizing on your heatsink helps radiate heat and you have the heatsink in the correct vertical orientation

Re: Converting the AC stick welder to DC
Posted: Fri Oct 28, 2022 7:20 am
by FUTZ
I wonder how DC a DC welder is? Never thought to scope one. It would be interesting to see the difference between a "bought" DC welder and Eugen's. When welding aluminum, isn't there a bit of AC on top of the dc?
Re: Converting the AC stick welder to DC
Posted: Fri Oct 28, 2022 11:01 am
by Eugen
FUTZ wrote: ↑Fri Oct 28, 2022 7:20 am
I wonder how DC a DC welder is? Never thought to scope one. It would be interesting to see the difference between a "bought" DC welder and Eugen's. When welding aluminum, isn't there a bit of AC on top of the dc?
My understanding, from reading around on the web, is that a stick welder needs a constant current DC, whereas MIG needs constant voltage. Regardless, looking at the schematic diagram of vintage DC stick welders, they don't have capacitors in the output, only a big choke. For those of us not really up to speed on electrical stuff, a choke is nothing more than a wire wound around an iron core. AC voltage oscillates 60 times per second from negative 170 volts to positive 170 volts. The full rectifier makes it so that it oscillates from zero volts up to 170 volts, but now 120 times per second. This is already called DC (direct current). However, it is not filtered. In the power supplies of audio hi-fi devices there is a lot of effort put into making the filtered DC be as close as possible to a constant voltage, like 12V for instance. The role of the choke in the stick welder is to be a buffer for current during the peak of the wave, and release it in the valley thus making sure the current is above zero amps.
@FUTZ if you are wondering how much better it is a "bought" DC welder than mine, it's probably a good deal better if you're talking about a quality unit like a Lincoln AC/DC. That is because they have a purpose built DC choke which will NOT saturate at full current. This is why I cut the core on the transformer I am using as choke, to make a gap. The gap in the core decreases the maximum inductance of the choke, but it allows it to have some inductance when big currents are passing through. Un-gapped cores will work well for smaller currents, but will saturate and have almost zero inductance (useless) for big current.
I have tested my welder last night with 1/8" 7018 rods with the welder dial on 165 amps. It worked very nicely. My understanding is that the 7018 rod works very badly when used on an AC welder. To me, this is the real test. The welds are smooth, and the 7018 electrode melts nicely and evenly.
I know nothing about welding aluminum, but from looking at some TIG machines, they always say that AC is needed if you want to TIG aluminum.